- Home
- SafyrOPC for Clean room monitoring
SafyrOPC for Clean room monitoring
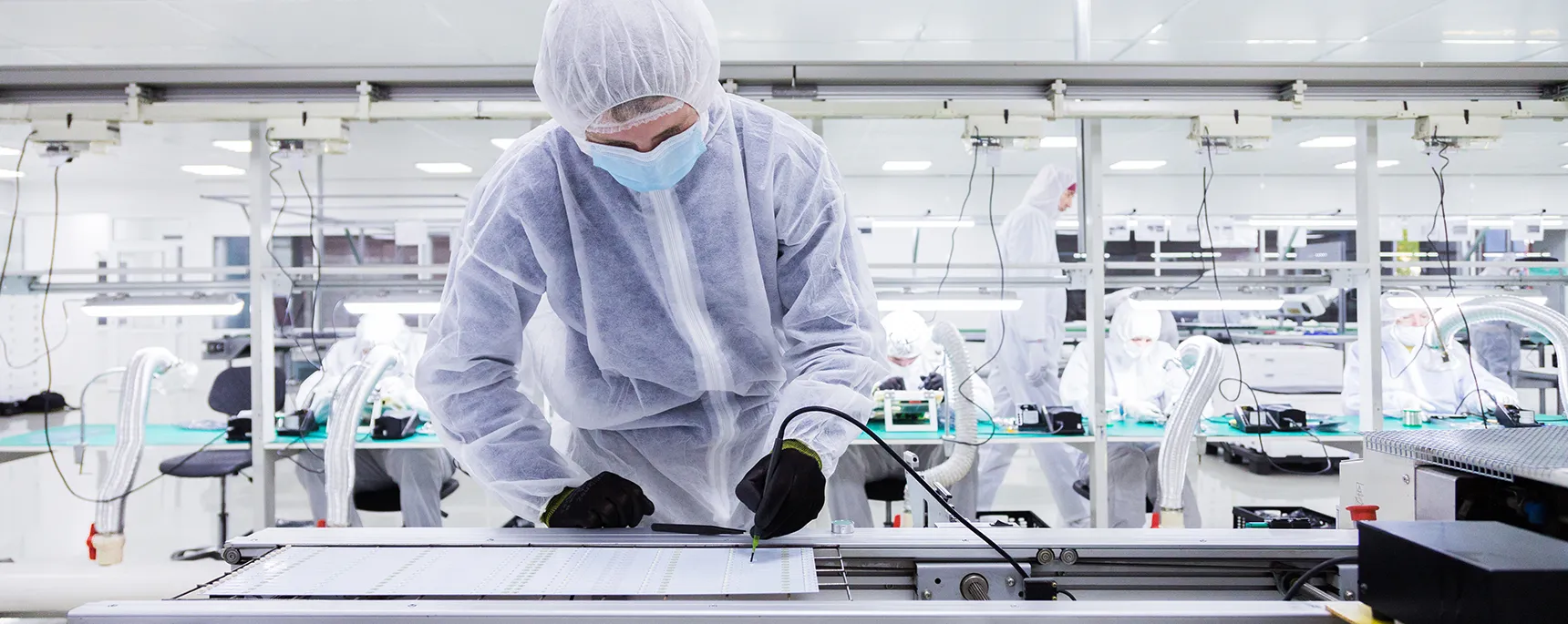
Real time particle counter for clean room safety
In industrial environments, particularly cleanrooms, fine particle airborne presence can significantly compromise process quality, product conformity and personal safety.
Controlling fine particles in cleanrooms is essential to maintain air quality in line with regulatory requirements, ensure the reliability of manufactured products and protect employee health. Sectors such as pharmaceuticals, electronics and food & beverage rely heavily on this rigorous control.
Addressing Air Quality Challenges in Clean Rooms
Clean rooms are specialized environments designed to maintain extremely low levels of airborne particulates, pollutants, and contaminants. These controlled environments are critical in sectors such as pharmaceuticals, biotechnology, electronics, and medical device manufacturing, where even the smallest deviation in air quality can compromise product integrity and safety. To maintain these standards, the ISO 14644 series sets the international criteria for clean room classification and monitoring, focusing on the control of airborne particulates and cleanliness.
Ensuring compliance with these standards is not only a technical necessity but also a regulatory requirement in many industries. Tera-Sensor’s NextPM solution provides advanced particle monitoring capabilities that help facilities achieve and maintain these stringent standards, ensuring product quality and safety.
Maintaining Air Quality Standards in Clean Rooms
Understanding ISO 14644 and Regulatory Compliance
The ISO 14644 standard defines the classification and requirements for maintaining air cleanliness levels in clean rooms. It categorizes clean rooms based on the maximum allowable concentration of particles of specified sizes. For example, an ISO Class 5 clean room allows no more than 3,520 particles per cubic meter that are 0.5 microns or larger. Deviating from these requirements can lead to product contamination, increased risk of batch failure, and potential regulatory penalties.
In the European Union, clean rooms used for pharmaceutical production must also comply with EudraLex Volume 4, which outlines Good Manufacturing Practices (GMP) specific to the industry. Monitoring systems that provide continuous real-time data on particle concentration are crucial for maintaining compliance with these standards and ensuring that the environment remains within the acceptable parameters.
Impact of Poor Air Quality on Clean Room Operations
Even small fluctuations in particle concentration can significantly impact clean room operations. Contaminants such as dust, bacteria, or chemical vapors can lead to defects in semiconductor manufacturing or contamination in pharmaceutical products. This can result in costly recalls, damage to reputation, and potential legal repercussions.
Benefits of Real-Time Air Quality Monitoring in Clean Rooms
Preventing Contamination and Product Loss
Contamination control is the primary reason for strict air quality standards in clean rooms. Particulate contamination can lead to product loss, reduced yield, and compromised product safety. For example, in the pharmaceutical industry, airborne particulate contamination can affect the sterility of products, making them unsafe for human use. Real-time air quality monitoring with sensors like NextPM provides early warnings of potential contamination, allowing operators to take immediate corrective actions before the situation escalates.
Enhancing Process Efficiency and Reducing Downtime
Maintaining air quality within the specified range also helps reduce the frequency of equipment maintenance and cleaning, leading to increased operational efficiency and reduced downtime. By using continuous monitoring, clean rooms can optimize their air filtration systems, ensuring that filters are replaced only when necessary, based on actual particle load, rather than on a predefined schedule. This data-driven approach can reduce maintenance costs and improve overall process efficiency.
FAQ
The NextPM sensor offers several benefits that make it a leading solution for particulate matter (PM) monitoring across various applications.
- High Accuracy: The NextPM sensor ensures reliable PM measurements with high precision, detecting particles as small as 0.3 µm and providing readings for PM1, PM2.5, and PM10.
- Wide Detection Range: It covers a broad range of particle sizes, from 0.3 µm to 10 µm, allowing for comprehensive monitoring of different pollutants in the environment.
- Durability: With a lifespan exceeding 20,000 operational hours, the NextPM sensor is designed for long-term use in demanding environments.
- Low Power Consumption: The sensor consumes less than 70mA in active mode and even less in sleep mode, making it energy-efficient.
- Adaptability: It features an internal heater that automatically activates to maintain measurement accuracy under high humidity conditions.
The NextPM sensor is equipped with an automatic heater system that activates when the relative humidity exceeds 60%. This feature ensures measurement consistency by reducing the effect of humidity on particulate matter readings. Users can also manually control the heater through specific commands if needed. Additionally, the sensor’s sleep mode function helps conserve energy by stopping all non-essential operations when activated.
The NextPM sensor supports two main communication protocols:
- Proprietary UART Frames: The default communication method, providing simple commands for reading and writing data.
- Modbus Standard Protocol: An industrial standard communication protocol that allows more flexibility and integration capabilities, especially in automated systems. This dual protocol capability enables the NextPM to be used in a variety of setups, from standalone operations to complex network integrations.
The NextPM sensor is robust and versatile, making it ideal for industrial applications where continuous monitoring and high reliability are required. Its features include:
- Resilience in Harsh Conditions: Capable of operating in temperatures ranging from 0 to +50°C and in non-condensing environments of up to 95% humidity.
- Compliance: The sensor is CE, REACH, and RoHS compliant, ensuring that it meets international standards for safety and environmental impact.
- Ease of Integration: With options for open or sealed casings, it can be seamlessly integrated into HVAC systems or standalone air quality monitors.